PROJECT
AMATHO (A.dditive MA.nufacturing T.iltrotor HO.using) is aimed to design, assess and manufacture a novel tiltrotor drive system housing exploiting the features of additive manufacturing techniques. Preliminarily, functional, structural and technological peculiarities of rotorcraft main gearbox housings are analysed and relevant requirements are issued.
In the meantime, viable AM processes are reviewed, on the basis of specific suitability, technological potential and degree of maturity. In particular, powder feed direct energy deposition techniques (Direct Laser Deposition – DLD) and powder bed fusion techniques (Selective Laser Melting – SLM and Electron Beam Meelting – EBM) are considered. The powder precursors are investigated as well, in terms of chemical nature (magnesium, aluminium, titanium alloy, stainless steel), particles granulometry and morphology. Static, fatigue, fracture mechanics, damage tolerance, corrosion endurance, chemical compatibility, machinability, weldability and heat-treatability testing are worked out and final trade-off process accomplished for choosing optimal materials and processes.
Characterisation methodologies and NDI techniques are assessed as well. In addition to test activity on dedicated specimens, smaller, but fully representative, full-scale gearbox housing components (to be considered as proof of concept) are manufactured through the traded-off technologies and tested to check the compliance with general functional aspects of r/c drive system housing. In parallel, design rules and methodologies for detail design, optimisation and structural substantiation of AM components are defined and supporting numerical tools are set-up. Full-scale housing is manufactured and structural and functional tests are performed to support flight clearance on the NextGenCTR Demonstrator and procedures (engineering cost and industrial capability assessment) for the start-up of high-volume production are also investigated.
WORKPLAN
WP1 – Feasibility Study & Preliminary Design [Months: 1-12] POLIMI
AIM
This task will enable to settle all data needed to reach the specification requirements. The main challenge will be to envisage the most suitable AM process, material and component design to meet all the requirements and boundary conditions defined by the NextGenCTR drive system layout. In addition, a knowledge base will be generated to support following activities. Finally, a joint Concept Review will be set-up at the end of Task1.
ACTIVITY
Review of precursor materials, AM technologies and main technical requirements of the final housing (functional, structural, interfaces, quality), in particular Evaluation from a design and manufacturing point of view of materials and their characteristics. Ti 6Al 4V (T1.2.1.2 – titanium alloys Ti6Al4V-like: granulometry, morphology, rheology) and Aluminum alloys (T1.2.1.1 – aluminium alloys, A356-like: granulometry, morphology, rheology) are the candidates to be considered.
SoA and identification of viable AM processes; definition and assessment of key performance indicators; generation of a knowledge base to support following activities.
WP2 – Material Characterization [Months: 4-45] POLIMI, SUPSI, PRIMA
AIM
The goal is to develop the processes and to assess their performances by means of:
(1) material and process characterization tests based on specimens of target materials;
(2) development of a small-scale prototype representative of the full-scale component;
(3) preliminary definition of design rules and assessment of numerical tools for topological optimization, simulation and modelling.
Test activities are aimed at describing the relationship between:
a) material properties and process/product performances;
b) process parameters and process/product performances;
c) design choices and product performances.
ACTIVITY
Design and test a set of coupons, both in agreement with AW standards. Coupons (> 1000) will be manufactured with most promising AM technologies and viable materials in order to perform a trade off. Main planned activities , aimed to assess feasibility and technical performances and characteristics of different solutions (powder/AM technique/pristine/defects/..), are:
T.2.1.1 Test Specimen Definition and Samples Production
T.2.1.2 Static and Fatigue properties characterization
T.2.1.3 Flaw tolerance and Crack growth characterization
The design and manufacture of an existing housing, adopting the AM technology will assess feasibility and technical performances and characteristics of a real (large, complex, ..) object.
Moreover the study and implement of advanced design methodologies, rules, SW tools and design optimization methodologies for topological structural optimization and structural substantiation will assess the application of numerical tools for design and optimization of real component.
WP3 – Detailed Design and Process Development [Months: 13-48] POLIMI, SUPSI, PRIMA
AIM
The WP covers three major aspects.
1) Study and implementation of advanced design methodologies for topological structural optimization and structural substantiation that are suitable for AM processes included into the trade-off analysis.
2) Definition and set-up of AM machine configurations for small scale and large scale prototype development.
3) Study and development of advanced in-process monitoring methodologies and configurations to rapidly detect and compensate process errors during the layer-by-layer process itself, to meet part and process qualification requirements
ACTIVITY
Structural optimizations allowed by AM will be applied to the drawings provided by AW, in order to fulfill the FRC gear-box housing design and structural optimization .
The process development implies to study and develop advanced in-process monitoring methodologies and configurations and to focus mechatronics aspects, like
– Methodologies for in-process monitoring for AM processes
– Product- and process- based requirement definition for the chosen process machine
– Laser source, optical system and machine configuration and set-up for the chosen processes
– Methodologies for design, optimization and structural substantiation of AM components
WP4 – Prototype and pre-production evaluation [Months: 38-60] PRIMA, POLIMI, SUPSI
AIM
The goal consists of designing, optimizing and manufacturing a full scale prototype by exploiting the knowledge acquired in previous tasks. The AM process for part manufacturing is the one (or two) resulting from the trade-off analysis previously performed. Structural and functional tests are carried out on the part. The objective of this WP is the identification of the product’s geometric features and the mapping to existing process technologies and parameters
The CAM produced in WP3 will be used to build the machine motion strategy. The monitoring and control loops will lead to an optimization process and a fine tuning activity. Evaluations for the start-up of the real production phase is performed at the end of the WP.
ACTIVITY
Manufacturing of the optimized FRC housings implies:
– Machine motion strategy design and path planning
– Machine control strategy design and configuration
– Machine in-line closed loop monitoring policy design and implementation
– Machine and process optimization for the manufacturing of final product demonstrator
In addition it will be given to AW the support to the full-scale test phase ,
providing AW with test plan proposal and advice and consultancy about testing and data collected.
Support the start-up of the production phase will also be given
WP5 – Communication, Dissemination and Exploitation [Months: 4-60] SUPSI, POLIMI, PRIMA
AIM
WP5 aims to set-out Project results and impacts. It is thus important to properly manage information and findings gathered during the Project, safeguardind IPR.
This WP will create awareness about primaries (AM) and ancillaries (Mechatronics, Laser, ..) technologies adopted in AMATHO, paying attention to business aspects
ACTIVITY
Spread in a effective and proper way (protecting IPR) findings relevant to AMATHO technologies by means of Internet, workshops and publication in scientific journals and major international conference. Moreover exploit results in academic, industrial and commercial environment. Create and update AMATHO Web site
WP6 – Project Management [Months: 1-60] POLIMI, SUPSI, PRIMA
AIM
WP6 will maintain the full control of progresses towards the project objectives as well as on the fulfillment of
all contractual obligations: Consortium Steering Committee (CSC, all partners represented), Project Management Committee (PMC, all WP Leader represented) will be the management key body. Management activities will be focused on two main directions:
1) To fulfill technical and financial contractual obligations toward CSJU2 and
2) To foster a good communication among partners and with the topic leader (AW), in order facilitate the project development and its successful outcome.
ACTIVITY
Identify proper key-role managers, decision mechanisms and management procedures. Organize CSC, PMC and review meetings;.
Fulfill technical and financial contractual obligations toward CSJU2, addressing all legal and contractual obligations
Foster a good communication among partners in order facilitate the project development and its successful outcome
Foster a good communication between the consortium and the topic leader (AW), in order to fulfil TL’s needs on the AM matter
Manage IPR and results protection activities
AM processes have witnessed notable development within the last decade, mainly owing to the recent developments in the laser sources, electronics and software capabilities. The industrial and research communties have contributed in the understanding of these technologies and their adoption in industrial manufacturing. At this stage, the research efforts have been mainly focused on evaluating the process capabilties
AMATHO identifies the following three components essentially important for the realization of large volume, small lot components by AM processes:
a) Precursor material
b) AM process
c) Post-processing
The final product conformity depends on the success of the chain of these three components, rather than treating them singularly.
As a matter of fact the correct precursor material choice will ensure good flowability and stable chemical characteristics during the AM process.
The correct choice of the AM process along with the use of optimized parameters will ensure part conformity as well as new functions provided by the AM process.
The materials produced by AM possess remarkably different characteristics under chip removal and welding processes, hence their complete intake and planning are fundamental for the successful implementation of the production chain.
These three components of AMATHO are investigated singularly by different groups in both industry and academy. Concerning the production of high-value single components by AM they need to be evaluated as a whole with their interactions.
a) Precursor material:
The most common precursor material in AM of metallic materials is powder. Several methods for powder manufacturing are available as depicted in Figure 2. The main characteristics of the produced powder are determined by the used manufacturing process. The chemical compositions, particle form, dimension and rheological characteristics rely on the used method. Gas atomization realizes spherical particles with reduced dimension (10-50 μm), with good chemical stability owing this to the inert processing environment. The use water atomization generates flakes with irregular shape and small to medium dimensions (30-80 μm).
These geometrical and chemical aspects of the powder have direct effect on the AM process, hence also on the product performance. The powder geometry determines its flowability, therefore how well it can be packed in powder bed or how well it can be blown from a nozzle. The chemical composition will also determine the final chemical composition of the AM product. For alloys, it is essentially important to pre-compensate the loss compounds with low vaporization point. During the AM process these compounds can be lost, so the final chemical composition deviates from the nominal one.
The interaction path described in Figure 12 is essentially important for determining the compatibility of the powder with the specific AM method to provide conformal components. The effect of powder characteristics on the AM product have to be defined with a clear connection between powder related parameters and product performance indicators. AMATHO, from this point of view, will determine the quality measures for powder characteristics that can be directly linked to the compatibility with AM processes and AM product performance. In particular, the following aspects will be quantified as described in Table 1.
b) AM Process:
In order to produce the final component, AMATHO will investigate the different AM processes for metallic materials. The AMATHO concept evolves around the idea of generating a tool rack based on the most promising AM methods for industrial production. AMATHO will firstly investigate the current capabilities in order to depict the current process capabilities for generating large size components. Moreover, the process capabilities for new functions on the final product will be identified. The conceptual tool rack will be constituted of two main types of AM processes:
i) High productivity AM processes able to realize large geometries. These processes provide means for manufacturing the entire component on a single machine or the base module on which smaller details can be added with other processes.
ii) High resolution AM processes able to realize new functions. These processes can be used in parallel to generate the large component in pieces, which can be later on assembled. They can be also used to realize component parts, where new functions such as light-weight lattice structures or internal channels are needed.
A pre-selection of the AM methods for the AMATHO’s tool rack is based on the state of the art. Several methods are available for additive manufacturing of metallic components. According to ASTM F42 standard five groups of technologies exist for additive manufacturing of metallic materials. Among these reported in Figure 3, the ones employing high energy beams are the most promising ones for rendering these technologies suitable for production purposes rather than prototyping. The two process families namely powder bed fusion and directed energy deposition make use lasers and electron beams, which provide highly concentrated energy sources. For AMATHO’s tool rack directed energy deposition (DED) processes constitute the high productivity processes, whereas powder bed fusion processes provide high resolution processes.
Together with the evolution of design rules, control systems and software capabilities these technologies exhibited a remarkable leap in their capabilities in the last decade. Today, their capabilities are being explored and application areas expanded. One of the main challenges these processes are facing is related to productivity and realization of components with large dimensions and large volume. The intrinsic advantage of layer-by-layer deposition that allows production of unique and complex components is difficult to be exploited, when the product size and hence the production time increases.
The working principles of AM processes based on high energy beams are schematically illustrated in Figure 4. Powder bed fusion technologies rely on the selective melting of each powder layer by the use of an energetic beam. This provides high geometrical resolution in both build direction and on the scan plane. Regarding these technologies, two possibilities emerge based on laser and electron beam use. The high speed deflection also allows for applying heating cycles on the powder bed before the melting cycle. This is an essential advantage to avoid internal stresses realized in process, especially in Ti alloys and alloys with high Ni content. For its proper functioning, the EBM processes requires vacuum, whereas SLM can work under an inert gas atmosphere. In directed energy deposition, the powder is blown over the deposition area, while the energetic beam is directed over the powder flux. The usual energy source for DED is laser, since it does not require vacuum environment and can be used in larger build volumes. Coupled to Cartesian axes or anthropomorphic robots, the process can be applied to build large volume components.
A more concise list of characteristics of the AM processes of AMATHO’s tool rack is presented in Table 2. The common difference between the powder-bed processes to directed energy deposition solution is the deposition rate. While, powder bed systems can build around 5-100 cm3/h, DLD systems can build up with higher rate (as a matter of fact the Borealis which is proposed in AMATHO should reach a rate of to 2000 cm3/hAMATHO). With all the present technologies, surface finish requires further machining for most of the mechanical applications (Ra>10 μm). Moreover most of the mechanical applications require further heat treatment and finally microstructure optimization. However, these factors are not a limitation for single batch productions, where machining and post-heat treatment are necessary for cast parts as well. Microstructural heterogeneity is common in the SLM and DLD products, due to the high cooling rates. By use of external heating systems SLM can be applied with pre-heating temperatures up to 200°C. Similarly, pre-heating can be used in DLD with temperatures up to 400°C, where the heating zone is commonly restricted to the deposition zone. The pre-heating eliminates the crack generation in Ti and Ni alloys. A post-heat treatment step is often applied to reduce internal stresses and obtain a homogenous microstructure. EBM process, from this point of view, is more advantageous. The warm process avoids rapid cooling cycles, hence the problems associated to them. Static and dynamic mechanical properties are reported to be desirable for all of the processes, once the microstructure homogeneity is obtained or maintained with the post-heat treatment step. It should be noted that these characteristics are well-established for small to medium sized components production. The maintenance of the process characteristics over large volumes of deposition needs to be identified.
Figure 5 illustrates the main advantages of powder bed and directed energy AM processes, employing commercially available machines. It can be seen that SLM and EBM processes can provide assembly within the build, hence moving parts can be obtained. The high resolution provides realization of complex and free form shapes. Light-weight structures and internal conformal channels are results of the high feature resolution obtainable. DLD, on the other hand, provides high deposition rate and the possibility of producing large parts. The directed powder flow means that, unlike powder bed processes, powder is used only where it should be melted. For SLM, the non-melted powder can be recycled, whereas for EBM this is not possible due to partially sintered powder within the pre-heat treatment cycle. Another important advantage of DLD is that it can be used to modify existing components or can be combined with foundry process to realize product variations on a common base. Borealis machine aims to exploit the best capabilities of the two families. As a matter of fact, with the DLD architecture, it will also implement strategies to generate powder beds using the deposition head and selectively melt where required.
AM process monitoring represents a key issue for the development of the AMATHO project. AM processes involve a long machining time for a single part and high value-added products, which makes post-process quality controls not sufficiently effective to achieve challenging quality, repeatability and capability goals. Therefore, in-process monitoring and real-time process control are necessary to keep under control the layer-by-layer evolution of the process and to adapt the process parameters to incipient errors detected in-line. The goal is to push the AM process development towards a zero-defect production, by considerably enhancing its repeatability and capability, which nowadays still represent two weak points of the technology, as pointed out by different recently published roadmaps [Errore. L’origine riferimento non è stata trovata.,Errore. L’origine riferimento non è stata trovata.]. The recent literature [Errore. L’origine riferimento non è stata trovata.,Errore. L’origine riferimento non è stata trovata.] demonstrated that several kinds of errors and defects may be detected during the AM process, which may have a detrimental impact on the dimensional accuracy, the surface finishing, the mechanical, physical and microstructural properties of the part.
AMATHO identifies two complementary and fundamental needs to face the challenging goal of defect mitigation and avoidance. The first need consists of the development and implementation of novel process monitoring methodologies and equipment to guarantee a fast and reliable detection of incipient defects and error onsets. The second need entails the development and implementation of novel in-process (real-time) adaptive control strategies. From a process monitoring perspective, several quantities are of interest. They include: the melt pool size, the melt pool geometry, the temperature distribution over the melt pool and the surrounding heat-affected zone, the temperature distribution and optical emission spectroscopy [7,8]. The monitoring systems can be divided into two major categories: co-axial monitoring systems and off-axial monitoring systems [9-12]. In coaxial monitoring configurations, the sensors exploit the optical path of the laser to gather information about the melt pool and the heat affected zone. In off-axial configurations, normal and/or infrared cameras are used to monitor geometrical and thermal characteristics of the entire layer.
Analogously to conventional machining processes, machine sensorization is necessary but not sufficient to achieve desired production enhancement goals via process monitoring. In-process signal/image processing, analysis and monitoring via statistical methods and/or machine learning methods represents one of AMATHO’s development pillars. AMATHO embraces the idea of extending, adapting and tuning statistical process monitoring methodologies, possibly coupled with machine learning paradigms, leading to novel solutions that comply with the requirements of different AM technologies. The main driving capabilities for the development and implementation of the monitoring system include:
• layer-wise reconstruction of each slice geometry for 2D and 3D comparison with the nominal geometry (CAD model),
• layer-wise detection and spatial identification of local defects by means of thermal measurements, either from co-axial or off-axial signal data,
• layer-wise detection of surface or contour patterns that may be symptoms of non-optimal scanning strategies or non-optimal process parameters,
• stability analysis from layer to layer of monitored quantities,
• detection of errors or malfunctions associated with the powder deposition.
An even more challenging framework regards the adaptive (real-time) control of AM processes. The quality of parts produced via AM depends on hundreds of controllable parameters, but it is also affected by different nuisance factors. The outcome of the in-process monitoring system may be used to adapt the process parameters to mitigate the onset of a defect and to avoid its propagation from one layer to the next one.
c) Post-processing:
The gear-box housing must accommodate, bearing seats, gears, shafts, which deserve interfaces with strict tolerances. These tolerances cannot be obtained in a single step by any technology (casting, milling and AM processes). This means that AM processes often have to be inserted within an existing production chain, where it may substitute some of the pre-existing process steps, as well as reducing the whole process cycle. However, both chip removal and assembly steps remain present within the production cycle.
AMATHO’s position with respect to the state of the art in conventional manufacturing of r/c components
The AMATHO project aims to provide means for substituting the main manufacturing process involved in the manufacturing of the specific product, the helicopter gear box housing. The gear box falls in the category of products that are characterized by large dimensions, stability under high temperatures and stringent mechanical properties that should be realized in small lots (typically two or a few). In order to fulfil the mechanical and thermal requirements these components are usually made of advanced engineering materials namely, Al, Ti and Ni alloys. Moreover, the geometrical restrictions allow only very few traditional manufacturing methods to be used. The use of sand casting method is the most feasible method among the traditional ones. Another casting option for instance, lost-wax-casting process is a usually a viable option for single lot manufacturing, but is preferred for smaller components. As a matter of fact it is not feasible in the case, since it relies on the generation of a ceramic shell for the mould. The large size of the component is most likely to be too heavy and break the ceramic shell during the process.
There are different steps that render casting prone to generation of large amount of scrap and eventually iterations are required to obtain the conformal product. The model and the peripheral components namely, risers, distributor channels and cores should be designed taking shrinkage, porosity, thermal distortions and other solidification related problems into account. Despite the more diffused use of simulation software for casting processes, the process still requires decision making based on experience. Accordingly, scrap generation due to an iterative phase before the conformal processing conditions is very common. For mass production parts, the effects can be distributed over the large production volume. However, for complex single products this fact becomes an important drawback. On the other hand, AM processes allow for a flexible manufacturing scheme. As depicted by Figure 9, the process is held over a digital environment from CAD to build phases. Moreover, the high resolution of the process allows for topology optimization tools for exploiting the light weight structure generation. Hence, before the actual build of the component the necessary iterations can be held in the digital environment, avoiding scrap generation.
In consideration of all the above, AMATHO proposal is ambitious and innovative and would provide advances beyond the state-of-the-art at least regarding three fundamental points of the activity:
a) issue and problem to be addressed (product): do develop, assess and produce a titanium alloy, large monolithic tiltrotor main drive system housing;
b) concept involved (process): adoption of DED – Directed Energy Deposition additive manufacturing technique characterized by very high deposition rate, deposition/ablation capability, very large monolithic devices manufacturing capability;
c) approach and method proposed (overall work organization): wide comparison of different viable metal powder precursors (Ti, Al) and different technologies (EBM, SLM, DED) and relevant trade-off; broad-range experimental evaluation (more than 1200 coupons involved) of the outcomes; comprehensive support to Topic Leader for a complete technology transfer.
Your Content Goes Here
Project reference: 717194
Call for proposals: H2020-CS2-CFP02-2015-01
Funded under: H2020-EU.3.4.5.3. – IADP Fast Rotorcraft
Start: 01 December, 2016; End: 30 November, 2021
Project duration: 60 months
Project Coordinator: Politecnico di Milano
Topic Leader: LEONARDO (Helicopters)
Ethics: Amatho team will work in permanent respect of Charter of Fundamental Rights of the EU.
This statement will be continuously guaranteed, in conformity to existing legislation and regulations, over the project life.
AMATHO TEAM
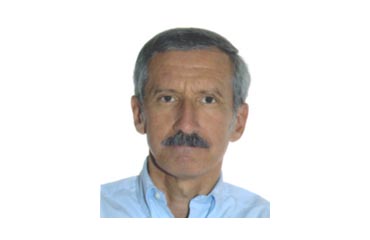
GIUSEPPE SALA
WP1
Feasibility Study & Preliminary Design [Months: 1-12]
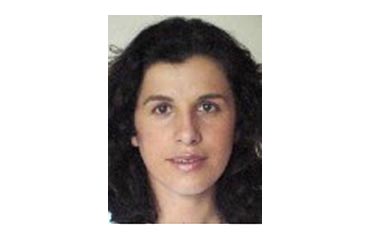
BARBARA PREVITALI
WP2
Material Characterization[Months: 4-45]
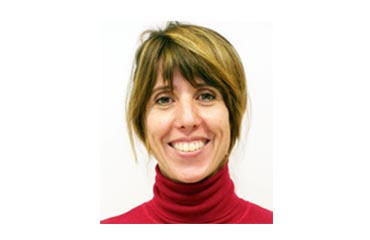
BIANCA MARIA COLOSIMO
WP3
Detailed Design and Process Development [Months: 13-48]
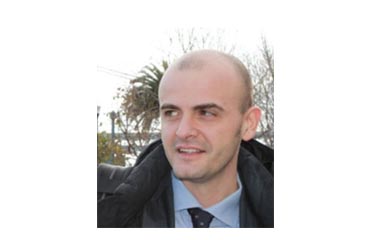
PAOLO CALEFATI
WP4
Prototype and pre-production evaluation [Months: 38-60]
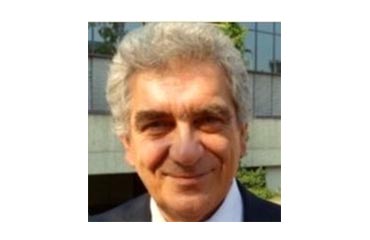
CORRADO CHIOZZINI
WP5
Communication, Dissemination and Exploitation [Months: 4-60]
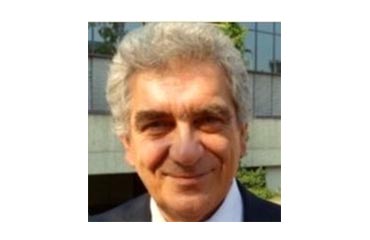